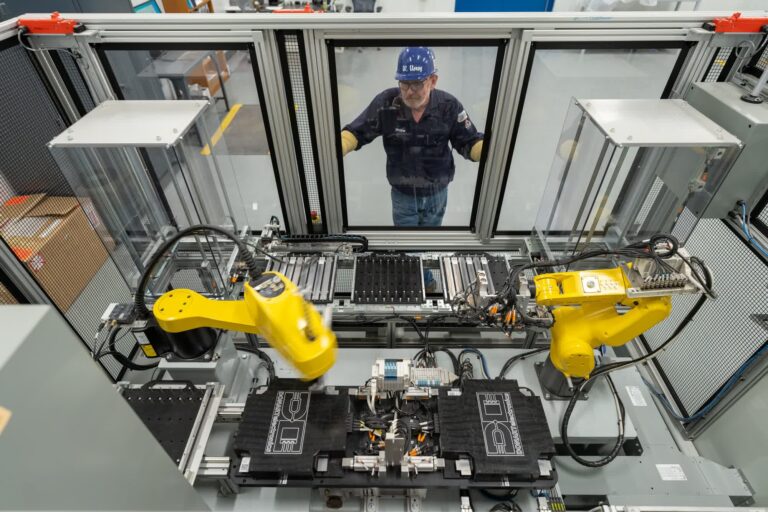
[ad_1]
Why it matters: Much of the current conversation surrounding electric vehicle manufacturing has focused on sourcing lithium for batteries. However, another critical component for EVs could come in short supply in the next few years—electrical steel. Manufacturers in the US are trying to ramp up production to compete in a foreign-dominated industry.
Analysts estimate that global supplies of electrical steel—needed for electric vehicle motors—could struggle to meet demand before the end of this decade. New companies are entering the market to avoid a crunch that could increase EV prices during a time when we need them to be more affordable.
Electrical steel is comprised of ultra-thin sheets that transfer electricity into mechanical power. Standard-quality electrical steel forms the core of the rotating motors powering things like washing machines, power transformers, power tools, or air conditioners. Electric vehicle motors and scientific measurement devices follow the same principle but require high-grade electrical steel, which is harder to source.
According to a Wall Street Journal report, making high-grade electrical steel is an exacting process, with lead times sometimes approaching a whole year. It involves stamping and stacking steel and silicon into precise shapes, sometimes under a quarter of a millimeter thick, so companies can’t simply buy their way into the market.
The overwhelming majority of electrical steel currently comes from South Korea, Japan, and China, all of which analysts say are under US steel import tariffs. Furthermore, global demand for high-quality electrical steel could exceed supply by hundreds of thousands of tons by 2027 and over a million tons by 2030.
American companies like Cleveland-Cliffs Inc. and US Steel Corp. are spending millions to open new electrical steel mills to help close the gap and raise the country’s competitiveness in this specialized sector. The company plans to have a mill up and running by the end of the year. However, it will likely take multiple years for domestic manufacturers to acquire the equipment and expertise to improve supply significantly. The resulting situation could put downward pressure on EV manufacturing.
The analysis contrasts with reports of falling prices for other EV raw materials, making the cars cheaper in the short term. Since January, prices of EV battery components, like lithium and copper, have fallen by around 20 percent. Tesla has passed the savings to consumers with five price adjustments this year. It’s unclear how long the situation will last or what will happen if it runs into electrical steel shortages.
[ad_2]