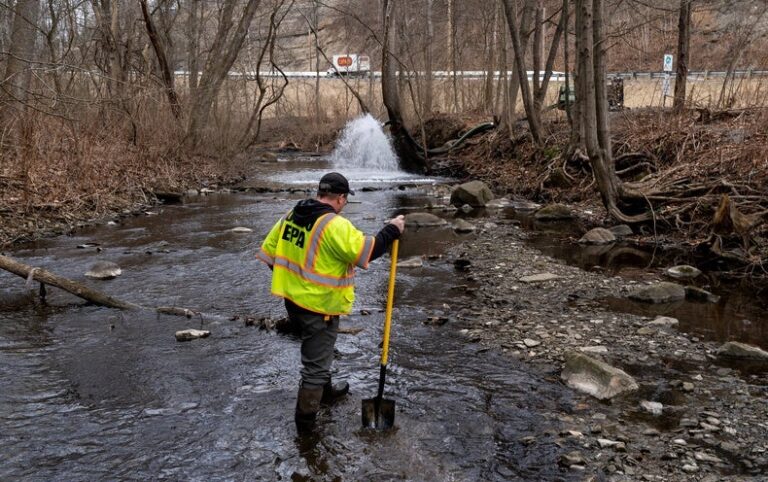
[ad_1]
As the story of the Norfolk Southern chemical spill in East Palestine, Ohio, continues to unfold, we are learning how this freight train derailment polluted local waterways and released hazardous contaminants into the air. People returning to their homes speak of health issues and dead pets, and the Environmental Protection Agency is now forcing the train company to pay for the cleanup. While this incident highlights the need for safer chemical transport, we believe what has happened is also a wake-up call for rethinking the chemistry that fuels our economy.
The cargo manifest of the freight train shows multiple cars contained combustible or flammable petroleum-based chemicals besides vinyl chloride. They include benzene and butyl acrylate, which are also precursors to plastics and other chemicals, as well as 2-butoxyethanol, a common ingredient in paint strippers and cleaning products. These chemicals include carcinogens, mutagens, reproductive system and organ toxicants, and skin and respiratory irritants. Fish kills in affected streams raise concerns about the long-term safety of drinking water and soils. And scientists are only beginning to look at persistent and toxic by-products, such as dioxins, created by the purposeful ignition of five tanker cars, in homes and soil. It is shocking that this cargo was not officially classified as hazardous.
If we want to end dangerous chemical incidents that make people and ecosystems sick, we need to address our dependence on these chemicals and the manufacturing processes needed to make them. This derailment and the chaos it has created must spur chemists, the chemical industry and the companies that rely on chemical products to create safer and more sustainable chemicals, processes, materials and products.
The current generation of chemicals that form the basis of our economy, including vinyl chloride and benzene, were rapidly developed, deployed and scaled prior to the 1960s. Their chemistries were built on increasingly abundant fossil-fuel platforms and designed for functionality and low cost. As “the industry of industry,” firms have used these chemicals to create new products and applications, in particular to create plastics, and to advance transportation, communications and construction technologies. Although environmental and occupational health laws of the 1970s and 1980s resulted in significant improvements in chemical safety, how we regulate these chemicals assumes that we can enjoy the benefits of what was transported by the derailed Norfolk Southern train while controlling the risks. But those risks can never be fully controlled.
The Ohio derailment was only one of more than 20,000 hazardous materials transport incidents that happen each year. More than 11,000 facilities across the U.S. make, use or store hazardous chemicals in amounts that could harm people or the environment, according to the U.S. Government Accountability Office. And 202 accidental releases happen per year on average at manufacturing, distribution and public works facilities. About one quarter of them affect nearby communities. The Environmental Protection Agency estimates the quantified annual damages from chemical accidents to be $434 million per year and the loss in property values caused by incidents in about 660 facilities from 2004 to 2019 to be $39.5 billion. Many of these facilities are located both in low-income communities of color and in areas with natural hazards that are likely to be exacerbated by climate change, increasing the potential for toxic chemical incidents in the future.
After several major chemical incidents, including the Union Carbide disaster in Bhopal, India, in the 1980s that killed thousands of people, a broad consensus emerged to change chemicals management strategies away from emissions controls, Tyvek suits, respirators and emergency cleanup plans. Preventing pollution at the source became a national priority with the 1990 Pollution Prevention Act. For many scientists and engineers, prevention at the source meant developing approaches to eliminate hazards by, for example, substituting dangerous chemicals in manufacturing processes with less dangerous ones or redesigning production processes and products to negate or dramatically reduce the use of toxic substances.
By the mid-1990s the concepts of inherent safety, green engineering and green chemistry emerged that applied the principles of pollution prevention to molecular and process design. A diverse group of experts recently developed a definition of sustainable chemistry as the “development and application of chemicals, chemical processes, and products that benefit current and future generations without harmful impacts to humans or ecosystems.” The European Union has also developed criteria for chemicals that are “safe and sustainable by design.”
Bringing together chemists and engineers with health scientists to better understand, evaluate, and eliminate environmental and health hazards at the design phase of chemicals and chemical processes will ultimately reduce hazards to workers, communities and consumers from production, transport, use, and end of life of chemicals and chemical products. Yet despite growing interest in sustainable chemistry in the research and education communities, industry and government have not fully embraced it.
Transitioning to safer and less hazardous chemicals and products is easier said than done. The chemicals and materials we have today—including polyvinyl chloride (PVC), the main use of vinyl chloride—are cost-effective, well performing and highly integrated into global supply chains. There is little incentive to transition, particularly given the significant costs of research and development, piloting, capitalization and reformulation to integrate new, safer chemicals into the economy—and little willingness from anyone to pay those extra costs.
We won’t adequately address the problems of hazardous chemicals without a supply of cost-effective and safer solutions. Rethinking the chemistries, manufacturing processes and materials that fuel our economy will require significant government coordination, investment, collaboration across industry, and meaningful engagement with academia and communities—the same concerted and sustained effort that built the current generation of chemicals. It will also require educating a new generation of chemists and engineers. Innovations in chemistry and chemical processes are critical to addressing the hazards of chemicals, but they can also address the industry’s significant contribution to climate change and plastics waste, which are increasingly under scrutiny from the investment community and government authorities.
The federal government has a unique opportunity to demonstrate leadership in advancing sustainable chemistry through its implementation of the Sustainable Chemistry Research and Development Act. And it can ensure that the massive investments made in manufacturing processes and materials to decarbonize the economy through the Inflation Reduction Act also address the toxicity and hazards of our current chemicals and materials. (The chemical industry is responsible for 20 percent of industrial CO2 emissions, according to the Department of Energy.) Research indicates that such investments would not only reduce the billions of dollars that toxic incidents cost us each year but would actually be beneficial to the economy, positioning the U.S. as an innovation and sustainability leader.
Designing, applying and scaling new chemistries and manufacturing processes will take significant time—likely decades—given cycles of research, development and manufacturing. But in the meantime, to avoid another East Palestine disaster, we need to enhance safety controls to protect communities and workers from such toxic tragedies. These safety controls include requiring electronic brake systems, expanding the number of well-trained safety-focused workers, and evaluating risks at facilities to adopt safer options when available.
The hundreds of people who were under mandatory evacuations have mostly returned to their community, which is now the focus of a massive hazardous waste cleanup operation. These people deserve immediate action to address this disaster. But for every community that has been or could be affected by hazardous chemical incidents, we need long-term sustained actions and investments to prevent such disasters by replacing hazardous chemicals with alternatives that are fundamentally safer to manufacture, transport and use.
This is an opinion and analysis article, and the views expressed by the author or authors are not necessarily those of Scientific American.
[ad_2]