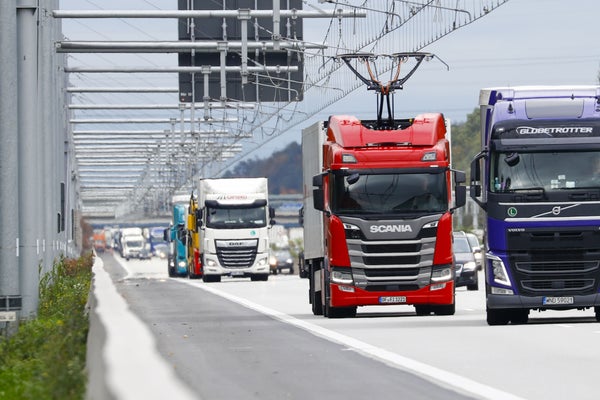
[ad_1]
Three Experiments Could Help Electrify Big Trucks
With a new EPA rule aiming to reduce carbon emissions from the biggest class of trucks in the U.S., companies are experimenting with overhead cables and wireless road charging
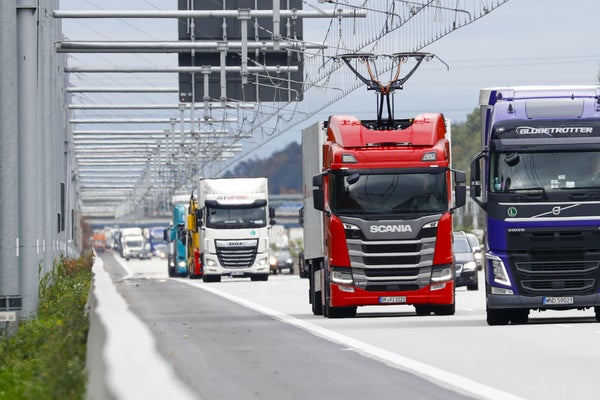
Overhead cable lines, wireless charging roads and battery swapping are three exploratory technologies to boost electrification of the trucking industry.
Alex Kraus/Bloomberg via Getty Images
CLIMATEWIRE | A climate rule for cargo trucks released by the Biden administration last week has put new pressure on makers of big rigs to cut their carbon pollution.
The industry might take cues from experiments that electrify semitrucks with overhead cables or wireless charging roads, or by swapping batteries at highway pit stops.
The EPA rule is expected to make about 17 percent of the biggest class of trucks in the U.S. carbon-free within eight years — a big test for vehicles that travel long distances with heavy loads.
On supporting science journalism
If you’re enjoying this article, consider supporting our award-winning journalism by subscribing. By purchasing a subscription you are helping to ensure the future of impactful stories about the discoveries and ideas shaping our world today.
“Electrifying trucks poses a much bigger challenge than replacing an internal combustion engine car with an electric car,” said Arjun Thangaraj Ramshankar, a Ph.D. student at the Georgia Institute of Technology who has studied the viability of using overhead cables for trucking.
Here are three experiments to watch as the freight industry undertakes a $1 trillion transition away from diesel fuel.
Overhead cables
Truck manufacturers could turn to a 140-year-old technology that has been used worldwide for city trams, passenger trains and public buses: overhead lines.
The so-called eHighway in Lübeck, Germany, and another pilot project near Los Angeles allow hybrid and electric trucks to suck power directly from the grid through pantographs extended from their roofs to overhead cables. When they need to change lanes or exit the highway, the pantographs retract automatically, and the trucks revert to engine or battery power.
“We just set up those cables on roads instead of railway tracks, and that’s the only difference,” Ramshankar said in an interview. “The setting is new, but the technology is the same.”
Anna Köhn, who manages public relations for the German project, said cables offer advantages over plug-in charging — which can require scheduling time to access chargers. It also gives drivers a dedicated lane or roadway, allowing them to avoid unpredictable traffic conditions, and it means they can keep moving as their batteries charge.
But there are downsides. The biggest hurdle is erecting the poles, hanging the cables and connecting them to the grid. The German Federal Ministry for Digital and Transport estimates that highway overhead cable infrastructure costs around $2.7 million per mile.
“There’s a lot of capital that goes into setting it all up before you can run trucks along the route,” Ramshankar said.
He co-authored a 2023 study that estimated freight trucks running on overhead cables would usually produce fewer carbon emissions than conventional electric trucks over their lifetimes. The economics are comparable and largely dependent on how widely the technologies are adopted, he said.
Wireless charging roads
Anyone who wirelessly charges their phone is familiar with inductive charging, a technique that uses electromagnetic induction to provide electricity to a device. Israel-based Electreon is now scaling that technology to power electric vehicles from underneath a road.
The company is testing inductive charging roads for heavy-duty electric trucks in Sweden and Utah plus several projects for passenger EVs throughout Europe, Israel and Detroit.
Electreon said it broke the world record for “the longest time and distance ever driven by a passenger Electric Vehicle” in 2023 when it drove a Toyota RAV4 Prime 1,200 miles over 100 hours on an inductive charging loop track built by the company in Israel. Company officials hope inductive charging can break the range anxiety that keeps some drivers away from EVs.
But just as phones charge slower wirelessly, wireless charging roads might struggle to support heavy-duty trucks. The Toyota RAV4 tested by Electreon is one-fifteenth as heavy as Tesla’s electric semi with a fully loaded trailer, and one think tank white paper warned that inductive charging may not supply “enough inductive power needed to drive trucks with large gross vehicle weight.”
Mike Roeth, executive director of North American Council for Freight Efficiency, an industry group, thinks overhead cables and inductive charging roads “would make sense in certain places,” but he expressed concern about the cost of both technologies.
The 1-mile inductive charging road in Detroit cost $5.9 million, according to the Michigan Department of Transportation.
Electreon did not respond to a request for comment.
Battery swapping
Roeth is more hopeful about a simpler means of charging electric trucks: replacing gas stations with areas to swap an empty battery for a fully charged one. “You build more batteries than trucks, and instead of fast-charging the batteries, you do a fast replacement of the battery,” Roeth said.
China is championing this approach, known as battery swapping. About half of the electric trucks sold in the country in 2022 were designed for the practice.
Yet battery swapping comes with its own complications. Roeth sees three main challenges with the practice: the cost of the extra batteries, ensuring a consistent standard of care for those batteries and potentially smaller batteries that are easier to move around. That could reduce a truck’s single-charge range.
Roeth says he’s uncertain what the future of trucking will look like and which electrification technology might prevail, yet he is convinced “basic efficiency will never go out of vogue.”
When Roeth meets with truck drivers and fleet owners, he advises them: “Don’t bet against batteries.”
Reprinted from E&E News with permission from POLITICO, LLC. Copyright 2024. E&E News provides essential news for energy and environment professionals.
[ad_2]