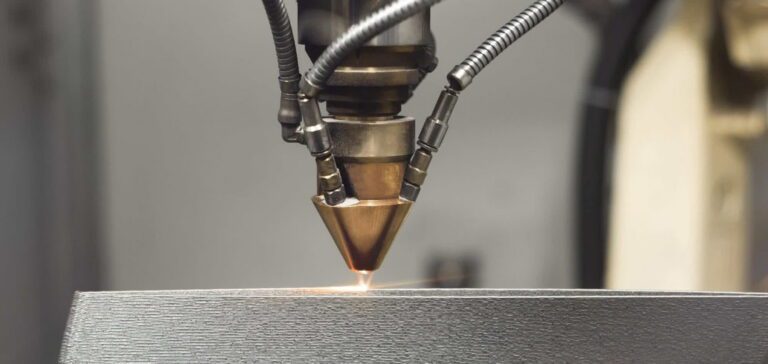
[ad_1]
Space Science: The recently launched Cygnus NG-20 robotic spacecraft is currently docked with the International Space Station (ISS). The resupply mission is packed with supplies for the ISS crew as well as science experiments, including an innovative 3D metal printer developed by Airbus for the European Space Agency (ESA).
In a historic development, the ISS is now equipped with a 3D printer capable of theoretically shaping new objects by melting stainless-steel wire. This experimental printer, designed by Airbus and ESA, serves as a means to test and address the technical challenges associated with metal 3D printing in space. It holds the potential to provide astronauts on future space exploration missions with innovative resilience and self-sustainment capabilities.
The 3D printer utilizes an industrial process known as additive manufacturing, one that has already revolutionized the design of parts and objects on Earth. While the ISS has several 3D printers using plastic material, metal printing presents different challenges, requiring a laser to reach the melting point of stainless steel (1,400 degrees Celsius), compared to the 200 degrees Celsius needed for plastic wires.
Ensuring the safety of the crew and the station is paramount, the ESA emphasized, requiring proper heat and fumes recycling. The printer operates within a fully sealed box, and the internal oxygen atmosphere must be replaced by nitrogen during printing to prevent oxidization of the metal parts being printed.
Once everything is up and running, the experimental machine will print “four interesting shapes” to test the printing process’s performance in microgravity conditions. The four designs are smaller than a soda can, weigh less than 250 g, and will take two to four weeks to print. The printer will operate on a schedule, as its fans and motors are “relatively noisy,” we’re told.
The final printed products will then be stored and returned to Earth, where they will be compared to reference prints created on the ground. Scientists will examine how the space environment can affect the printing process, providing invaluable insights into how the technology can be improved to become an integrated part of future space missions.
Tommaso Ghidini, head of the mechanical department at the ESA, stated that the opportunity to print metal parts in space is a “promising capability” that can support the future of space exploration – on the ISS and “beyond.” Thanks to in-situ manufacturing, astronauts could one day repair or augment space structures on otherworldly settlements like the Moon or Mars, eliminating the need to wait for costly, lengthy shipments of spare parts from Earth.
[ad_2]